Machining certain materials such as stainless steel and titanium can be difficult and challenging when you only own a small CNC machine. They are tougher than the usual wood and plastic many small CNC machines work on. However, if you have the correct feeds and speeds, your little machine can work on almost any material you want.
Despite having a smaller machine, you can still use some of the same tooling as that of a larger, stronger VMC. Doing some small adaptations, such as popping a premium end mill into your CNC machine can make all the difference. For more further insight and tips on how to machine tougher materials with your smaller machine, click here: The 12 Secrets of Machining Tough Materials on Small CNC Machines.
Even though Boss is primarily a laser company that sells CNC laser machines, we also have extensive experience with CNC router machines. Our experts can make recommendations and offer helpful tips we’ve learned from processing materials on our own CNC routers. When working with hard materials like dense hardwoods, abrasive plastics, or metals, using the proper tooling is crucial.
In this blog, we’ll explore valuable tips for small CNC machines when handling tough materials, providing insights and practical advice to help you overcome these challenges and achieve precision and quality in your machining projects.
What Are CNC Machines?
Computer Numerical Control (CNC) is a technology that uses computers to control and operate machines. This technology allows for high precision and efficiency in manufacturing different products. CNC machines can work with a wide variety of materials, from metals to plastics, and even wood.
Working with certain materials like hard and brittle ones can present unique challenges because these materials have low ductility and high hardness, making them prone to cracking and thermal shock. Their machining requires careful optimization of various parameters, such as feed and speed.
Here are some tips to ensure smooth machining operations on your small CNC machine.
Understanding Material Behavior
The first step in overcoming CNC machining challenges is understanding the behavior of the material you’re working with. Hard and brittle materials, like ceramics, glass, and carbides, are characterized by low ductility and high hardness. They resist deformation under stress but are also prone to cracking and thermal shock.
To effectively work with these materials, you need to comprehend how they react under varying temperatures, pressures, and vibrations. You should then adjust your cutting strategies accordingly. For instance, you can opt for a low depth of cut, high spindle speed, and intermittent cutting. Be cautious when machining unknown materials, as they may have unexpected properties that can affect cutting performance. Adjust feeds, speeds, and tooling based on the material’s behavior.
Choosing the Right Tool Material and Geometry
The success of your CNC machining process largely depends on the tool material and its geometry. Your tool should exhibit high hardness, excellent wear resistance, and impressive thermal conductivity. Considering the appropriate number of flutes for the material you’re machining is crucial to prevent issues like chip buildup and tool breakage.
When it comes to tool geometry, you should aim for a sharp edge, a large rake angle, a small clearance angle, and a small nose radius. These features help reduce the cutting force, friction, and heat generation, making your process more efficient and the end product higher in quality.
Optimizing Feed Rate and Spindle Speed
Using proper feeds and speeds is crucial for preventing cutter breakage. Ensure you’re using a feeds and speeds calculator and avoid going too slow, which can cause rubbing and excessive heat buildup. The feed rate should be low enough to avoid excessive force and vibration. However, it should also be high enough to prevent tool rubbing and overheating.
On the other hand, the spindle speed should be high enough to achieve a fine surface finish and reduce the contact time. Yet, it should be low enough to avoid thermal shock and tool wear. You can calculate the optimal feed rate and spindle speed based on the material hardness, tool diameter, and cutting depth.
Importance of Coolant and Lubricant
Coolants and lubricants are essential in CNC machining of hard and brittle materials. They help in reducing the cutting temperature, friction, and chip adhesion. Also, they improve the tool life and surface quality of the product.
It’s crucial to note that not all coolants and lubricants are suitable for every material. For instance, water-based coolants are ideal for ceramics and glass, while oil-based lubricants work best for carbides and CBN tools. Certain materials, like aluminum, require lubrication to prevent the cutter from welding to the material. Using a mister or coolant system can help keep the cutting area lubricated and prevent tool damage.
Monitoring and Maintaining Tool Condition
The condition of your tool significantly impacts the feed and speed parameters in CNC machining. Tool wear, damage, and deformation can reduce cutting efficiency and increase the risk of tool failure and material cracking. When using small diameter cutters, exercise caution as they are delicate and prone to breakage.
It’s important to monitor and maintain the tool condition regularly. This can be done through visual inspection, force measurement, acoustic emission, or vibration analysis. It’s also necessary to replace or sharpen the tool when it reaches a certain wear limit or shows signs of deterioration.
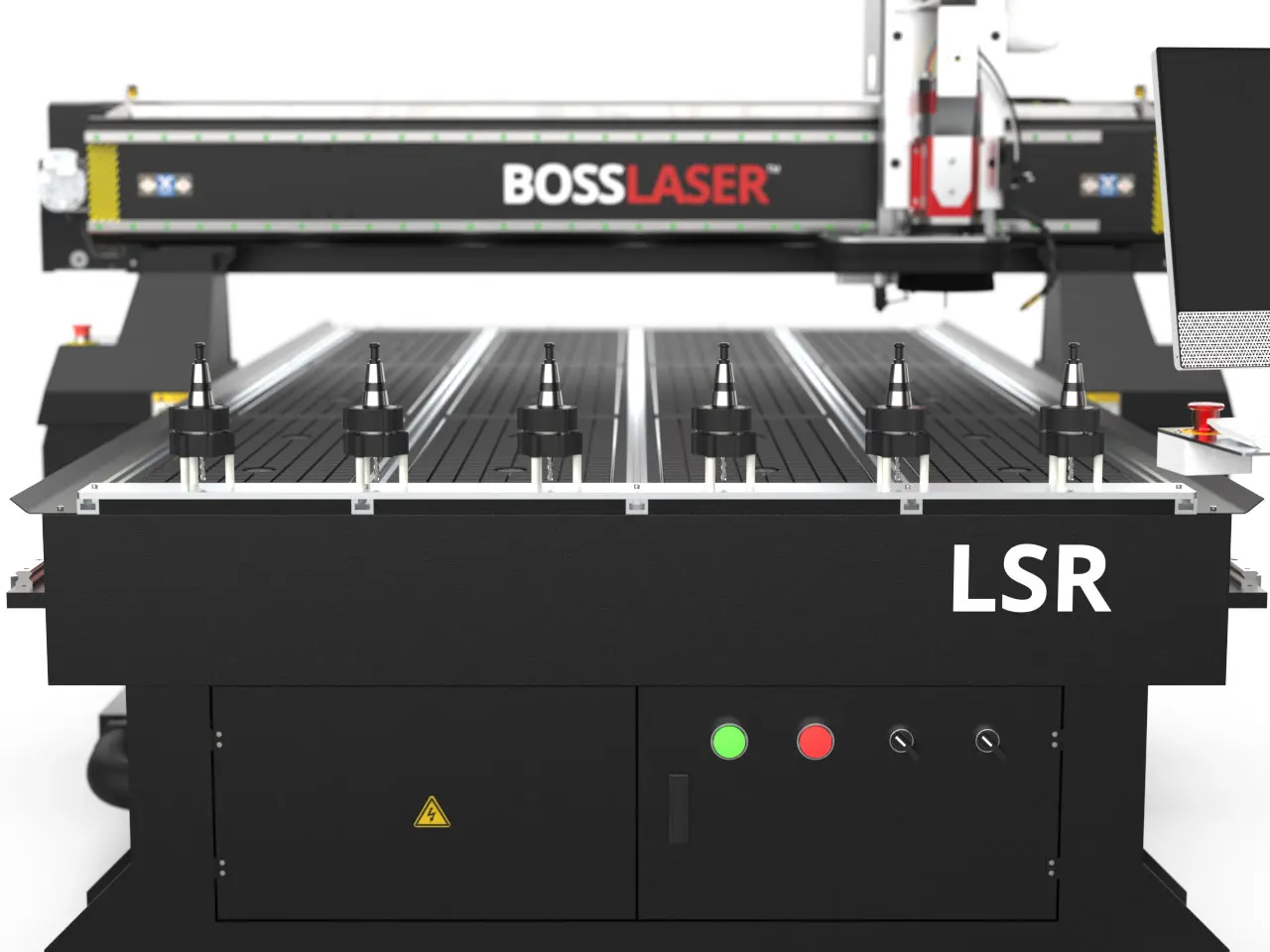
The Need for Experimentation and Optimization
The feed and speed parameters for CNC machining are not fixed. They depend on various factors, such as material composition, tool design, machine performance, and environmental conditions. As such, you need to experiment and optimize the process based on your specific situation. Techniques such as trial-and-error, design of experiments, or simulation can be very beneficial.
Additional Tips for Small CNC Machines When Handling Tough Materials
Here are more tips to keep in mind for smooth machining operations on your small CNC machine:
- Too Much Runout: Check for runout in your spindle and toolholder, as excessive runout can cause uneven cutting forces and premature tool wear. Replace any toolholders with high levels of runout to maintain machining accuracy.
- Poor Chip Clearing: Proper chip clearing is essential for preventing chip buildup, which can lead to cutter breakage. Use flood coolant or strong mist/air systems to ensure chips are effectively removed from the cutting area.
- Machine Rigidity: Ensure your CNC machine is rigid enough to handle the cutting forces involved. Minimize machine flexing by derating the machine’s horsepower and optimizing toolpath strategies.
- Setup Rigidity: Secure your workpiece properly to prevent slippage during machining. Use clamps or fixtures to hold the workpiece securely in place and minimize vibrations.
- Smooth Cut Entry: Use helical or ramping entry methods instead of plunging straight down to prevent cutter chipping and breakage during entry.
- Spindle Stalling: Avoid overloading the spindle by using feeds and speeds calculations that consider the spindle’s power curve. Monitor spindle load to prevent stalling and cutter breakage.
- Incorrect Part Zero and Tool Length Offset: Ensure your part zero and tool length offsets are set correctly to prevent cutter collisions and premature wear.
- Backlash: Check for backlash in your machine’s ball screws and adjust as needed to minimize unwanted motion during cutting.
- Tool Deflection: Minimize tool deflection by using appropriate cutter sizes and reducing cutting forces. Consider using shorter tools or reducing cutting depths to mitigate deflection effects.
- Using an End Mill: Premium end mills are engineered with advanced materials and cutting-edge designs that offer superior performance and durability. Their precise geometry and high-quality construction allow them to efficiently handle larger materials with ease, minimizing the risk of tool deflection, chatter, and breakage.
Contact Boss Laser
Tougher materials require more robust and sharper cutting tools that can withstand the increased cutting forces without premature dulling. With the right setup and techniques developed through our experience, even the most challenging materials can be precisely machined on a small CNC router.
By following these tips and addressing potential issues proactively, you can minimize cutter breakage and optimize your small CNC machine’s performance when handling tough materials.
Contact Boss Laser today to discover how our cutting-edge laser technology can elevate your CNC machining projects to new heights of precision and excellence.