Many materials require some form of lubricant when being used on a CNC machine. A proper coolant is also needed to prevent CNC machines from getting overworked. It is important that you do your proper research in order to find a lubricant and a coolant that will prevent your CNC machine from overworking a piece of material, overheating a work piece, and preventing the work piece’s material from bonding to your CNC machine tool. With that said, be sure you have a proper enclosure on your CNC machine to prevent a mess of liquid. Check out why you need an enclosure here: The 17 Cent Flood Coolant Enclosure
Even though Boss is a laser company and sells CNC laser machines, our experience extends beyond lasers to include CNC router machines, allowing us to offer valuable recommendations and tips that cater to the needs of CNC operators across various industries. So, whether you’re a seasoned CNC user or considering expanding your shop’s capabilities with a laser machine, check out these helpful tips we have learned from our experience processing materials on our own CNC router machines.
By understanding the importance of these elements and implementing best practices, you can optimize your CNC and laser machining operations to achieve exceptional results.
The Role of Lubrication & Coolant in CNC Machining
Lubrication is a fundamental aspect of CNC machining that involves the introduction of a lubricant between the cutting tool and the workpiece. The primary purpose of lubrication is to reduce friction and heat generated during the machining process. By minimizing friction, lubrication helps to prevent tool wear, tool breakage, and workpiece damage. It also facilitates smooth chip evacuation and ensures the accuracy and precision of the machining operation.
Coolant serves the critical function of heat dissipation during CNC machining. As the cutting tool interacts with the workpiece, significant heat is generated, which can lead to thermal expansion, tool deformation, and poor surface finish. Coolant is designed to rapidly remove this heat from the cutting zone, maintaining a stable temperature and preventing thermal damage. It also helps in chip evacuation, lubrication, and corrosion protection.
Types of Lubricants and Coolants
Lubricants
- Oil-based lubricants: Oil-based lubricants, typically composed of mineral or petroleum-based oils, are widely used in CNC machining. These lubricants offer excellent lubrication properties and can withstand high temperatures. They provide a protective film on the cutting tool, reducing friction and wear.
- Solid lubricants: Solid lubricants, such as graphite or molybdenum disulfide, are often used in specific applications where conventional lubricants may not be suitable. These lubricants have low friction coefficients and can withstand extreme temperatures and pressures.
Coolants
- Water-based coolants: Water-based coolants, also known as cutting fluids, are the most used coolants in CNC machining. They are composed of water mixed with various additives to enhance their cooling and lubricating properties. Water-based coolants are cost-effective and provide excellent heat dissipation.
- Synthetic coolants: Synthetic coolants are chemically engineered fluids designed to provide superior heat transfer capabilities. These coolants are resistant to bacterial growth and offer extended tool life. However, they may be less effective in terms of lubrication.
- Semi-synthetic coolants: Semi-synthetic coolants, as the name suggests, are a combination of synthetic and oil-based coolants. They offer a balance between heat transfer and lubrication properties, making them suitable for a wide range of machining applications.
- Minimum Quantity Lubrication (MQL): MQL is a technique that uses a minimal amount of lubricant, typically in the form of a fine mist or aerosol, to reduce friction and dissipate heat. This technique minimizes coolant usage and waste while providing sufficient lubrication.
Benefits of Lubrication and Coolant in CNC Machining
Enhance your CNC machining process with the benefits of lubrication and coolant:
- Heat management: Lubrication and coolant play a crucial role in controlling the heat generated during the machining process. By dissipating heat, they prevent thermal damage to the cutting tool and workpiece, ensuring dimensional accuracy and surface finish.
- Tool life extension: Proper lubrication reduces friction and wear on the cutting tool, leading to extended tool life. Coolants also contribute to tool life extension by maintaining optimal operating temperatures and preventing tool degradation.
- Chip evacuation: Lubrication and coolant aid in chip evacuation by flushing away chips and debris from the cutting zone. This prevents chip accumulation, which can cause poor surface finish, tool breakage, and workpiece damage.
- Lubrication: Lubrication reduces friction between the cutting tool and the workpiece, minimizing wear and improving machining efficiency. It ensures smooth chip flow and helps prevent chip welding and built-up edge formation.
- Corrosion protection: Coolants provide a protective barrier against corrosion, safeguarding both the cutting tool and the workpiece. This protection is essential, especially when machining materials that are prone to oxidation or chemical reactions.
- Surface finish improvement: Proper lubrication and coolant usage contribute to achieving a superior surface finish on the machined parts. They reduce the likelihood of heat-related distortions, burn marks, and surface irregularities.
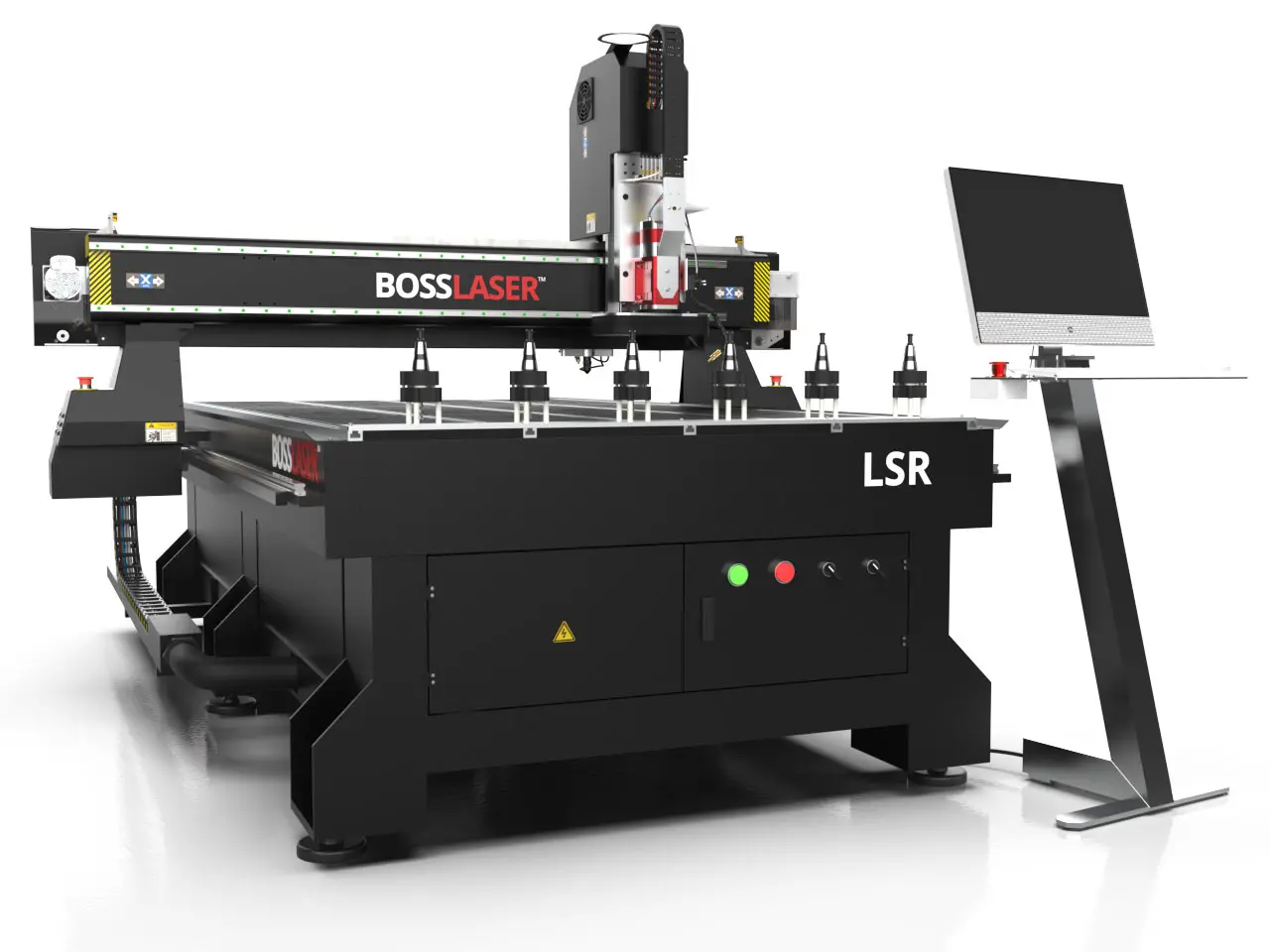
Lubricant and Coolant Selection for Your CNC
When selecting lubricants and coolants for CNC machining, several factors should be considered:
- Material compatibility: Consider the compatibility of lubricants and coolants with the materials being machined. Some materials may react adversely to certain lubricants or coolants, leading to undesirable effects.
- Environmental considerations: Evaluate the environmental impact of lubricants and coolants, such as their toxicity, biodegradability, and disposal methods. Choose environmentally friendly options whenever possible.
Maintaining the proper concentration of lubricants and coolants is crucial for optimal performance. Regular monitoring and adjustment of concentration levels ensure the desired balance of lubrication and cooling properties. Improper concentration can lead to decreased performance, tool wear, and potential workpiece damage.
Implementing effective filtration systems helps remove contaminants, such as chips and debris, from the lubricants and coolants. This enhances the longevity and performance of the lubricants and coolants, reducing the need for frequent replacements.
Adhere to health and safety guidelines when handling lubricants and coolants. Some lubricants and coolants may contain hazardous substances that require proper protective measures. Ensure proper disposal and recycling practices to minimize environmental impact.
Contact Boss Laser for CNC and Laser Machines
Lubrication and coolant are integral elements in CNC machining, contributing to the efficiency, precision, and longevity of the machines and the quality of the final products. Proper lubrication and coolant management not only enhance performance but also contribute to a safer and more environmentally conscious workspace. Although Boss primarily sells CNC laser engraving machines, our expertise spans CNC router machines as well, enabling us to provide valuable recommendations and tips tailored to CNC operators across industries. If you’re looking for assistance servicing your machine or are in the market to purchase a laser, check out our variety of machines and how Boss Laser can take you to the next level.